製品設計の思想…目先だけでなく、将来的なバージョンアップを見越した共有化を
品質改善
2021.12.01
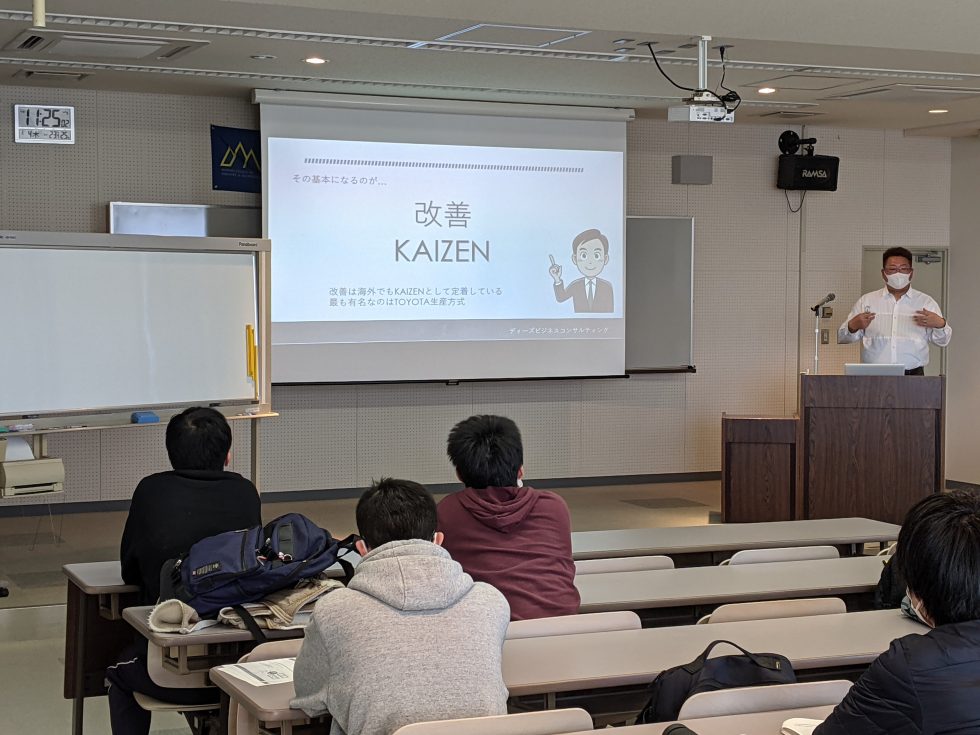
地域活性化の為に魅力ある地方企業づくりのお手伝いをさせて頂く、
ディーズビジネスコンサルティングの佐藤です。(‘◇’)ゞ
株価大幅下落。
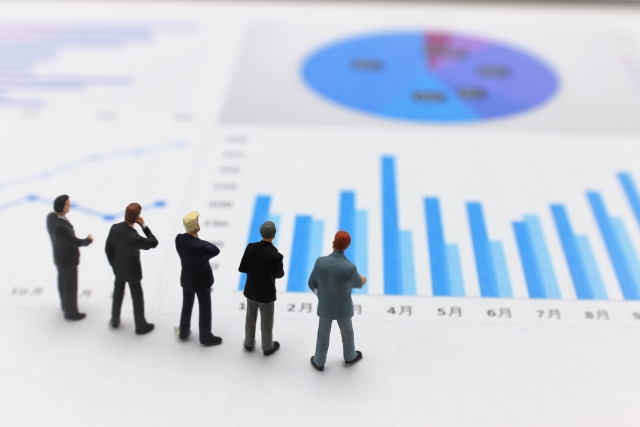
オミクロン変異株の警戒で、株価急落が起きています。
日本でも、今日時点で2例の感染報告がされています。
原油価格の高騰、アメリカFRBの金利施策等もありますから…。
また、下がりそう。
頭の痛いところです。
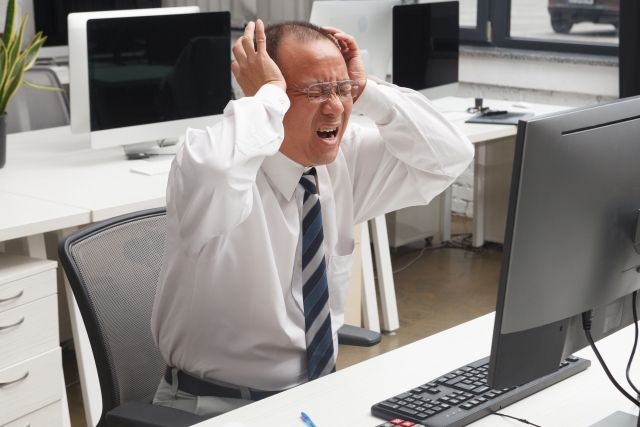
でも、短期で見るだけでは、投資は上手く行かないもの。
日々の推移だけ見て、嘆いていても仕方ない。
投資先の経営状態、中長期計画などの将来性を見て、耐える時は耐えないと…。
ここが難しいところですが…。
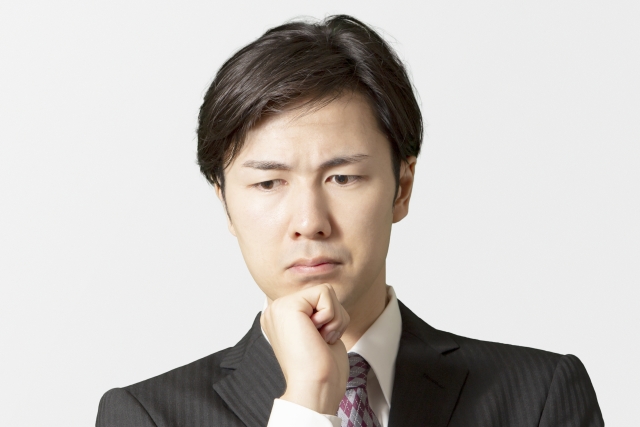
将来性。
これは会社という、大きな括りだけでなく、製品開発にも関わるところ。
大概の工業製品は、派生機種が出てきます。
これを想定して開発するか、否か。
これで将来の採算性は、大きく変化します。
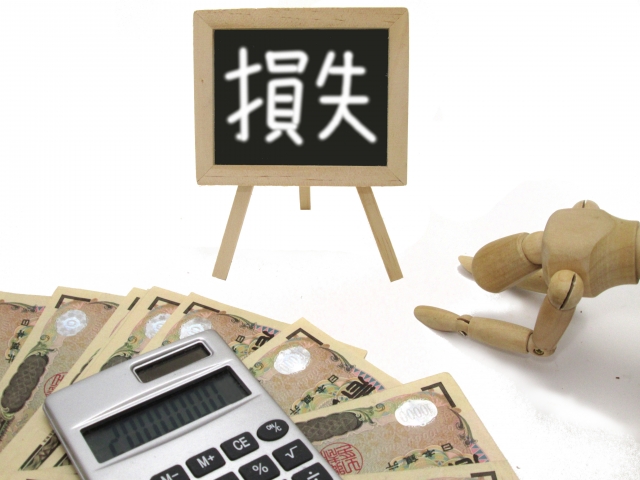
特に注意したいのが、材料の共有化。
例えば、基板について考えて見ましょう。
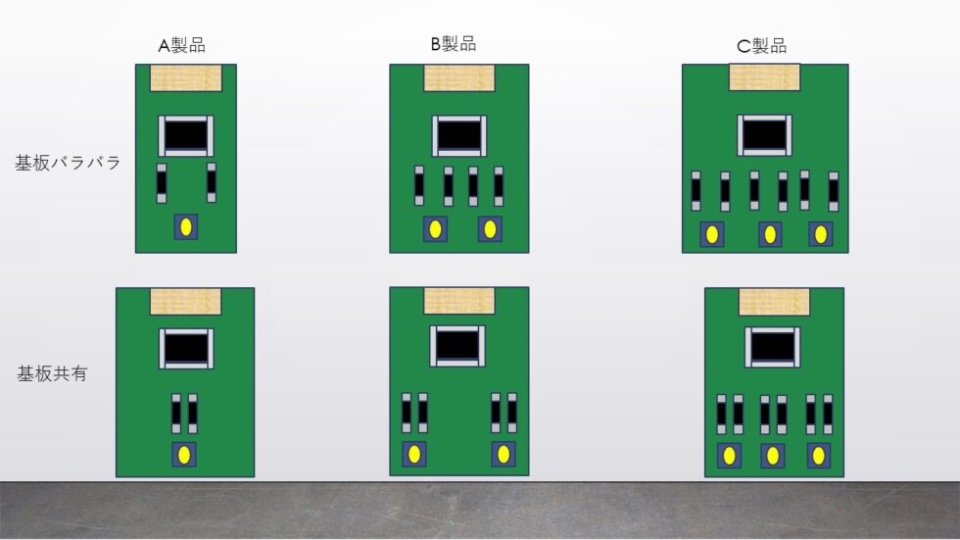
上の様に、製品が増えるたびに、基板サイズアップする。
どんな将来的な無駄を生むか、想像できますか?
ちょっと考えて見ましょう。
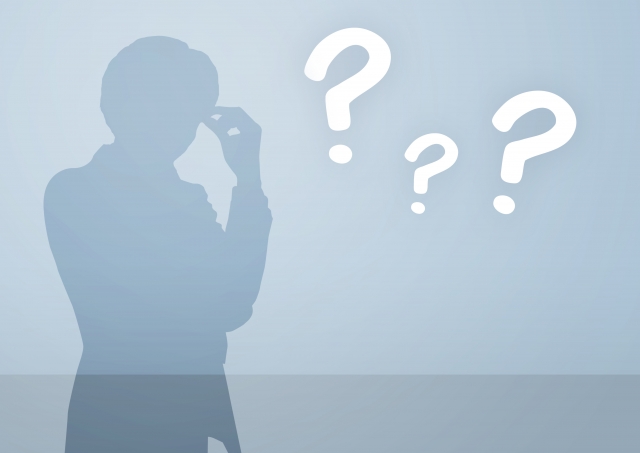
どうですか?
イメージできましたか?
沢山の無駄が想定できますが、一部記載して見ましょう。
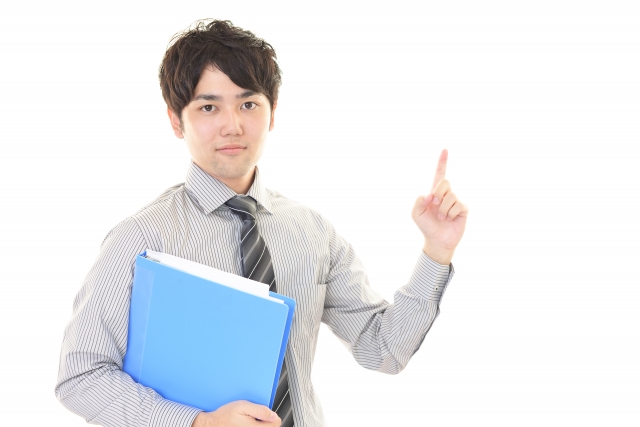
一つ目は、仕入れ。
基板メーカーへの発注が3タイプ。
基板メーカーは、タイプ毎に回路設計して加工。
当然、コストも上がります。
仕入れた後も、タイプ別に在庫管理する、という無駄も。
二つ目は、加工。
基板サイズが異なることで、セットアップに段取り替えが必要になり、設備停止時間が増える。
設備の仕様によっては、タイプ毎に設備を作らないと…。
三つめは、副資材。
梱包形態の副資材も、タイプ毎に型を起こす必要があります。
こちらも、コストアップの要因。
当然、仕入れ後の管理も。
これ以外にも、まだまだ無駄が、想定されます。
品質にも、必ず影響出ます。
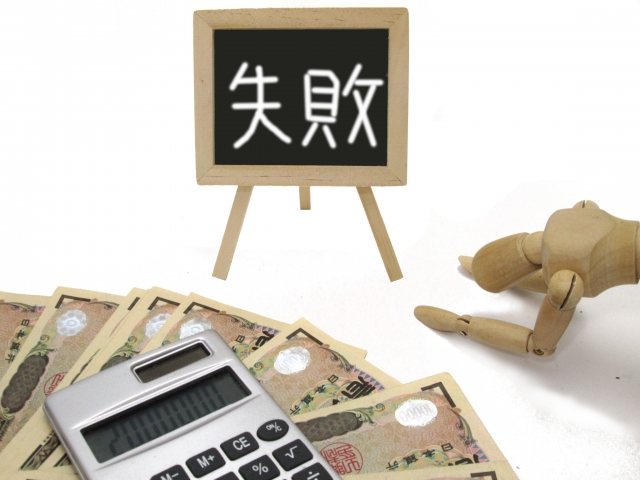
派生製品を最初に描いていれば、どうなりますか?
下段の様に、基板を共有化する設計をしていたら?
色々な無駄が、未然に防げるはずです。
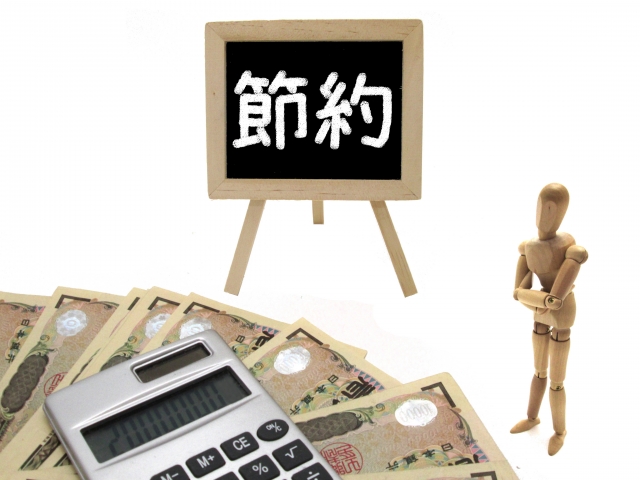
どうすれば、この様な無駄を防げるか?
製品企画段階で、派生の可能性を判断するルールを作ることです。
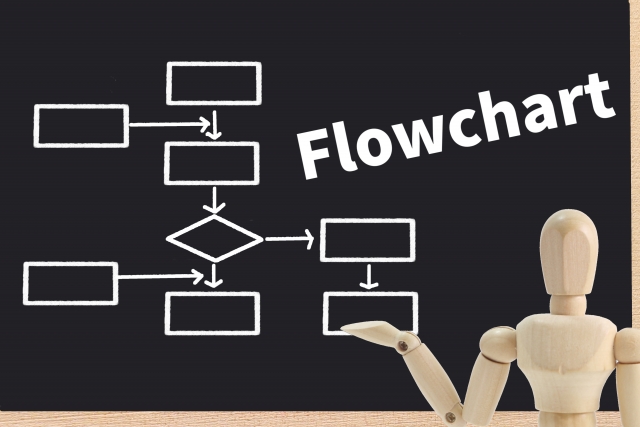
調査内容、判断条件等をフローチャートにする。
派生機種立ち上げの可能性が高ければ、設計開発時点で、部品共有の思想を入れる。
この様な仕組みを構築できれば、将来の無駄に対する、未然防止になります。
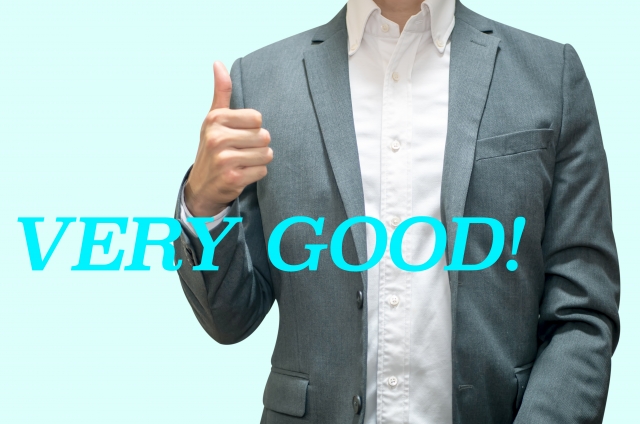
「うちは、自社で設計していないから…」
その場合、提案することも考えましょう。
どのみち、将来的にコストダウンの要請は、必ず来ます。
その時に、winwinの関係になれる…なら、話しを聞いてもらえると思います。
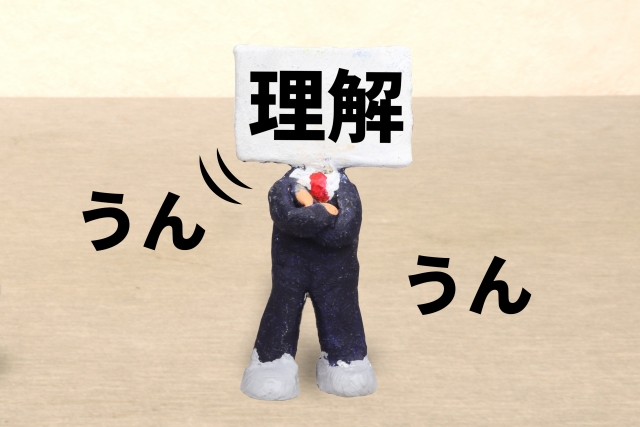
そして、この部品共有化の設計思想には、改善知識が不可欠。
改善に対する知識があるか、否か。
これで、出来栄えと結果が、大きく変わります。
改善は、今あるものだけを変えるものではなく、新たに生み出すものにも、影響を与えるものです。
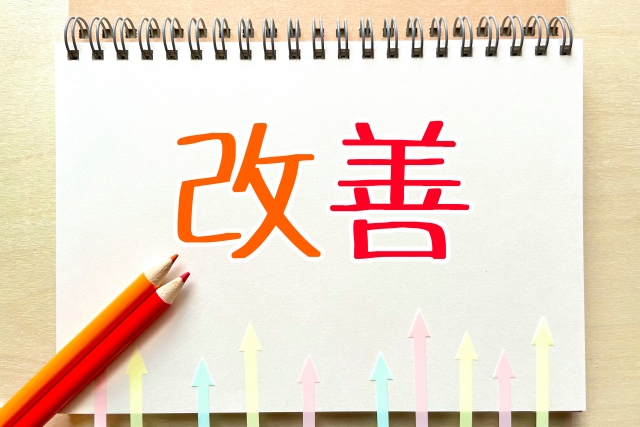
こんな課題を解決したい…、ぜひ、ご相談下さい。
儲かる仕組みづくりの、お手伝いをさせて頂きます。
See you tomorrow ♬
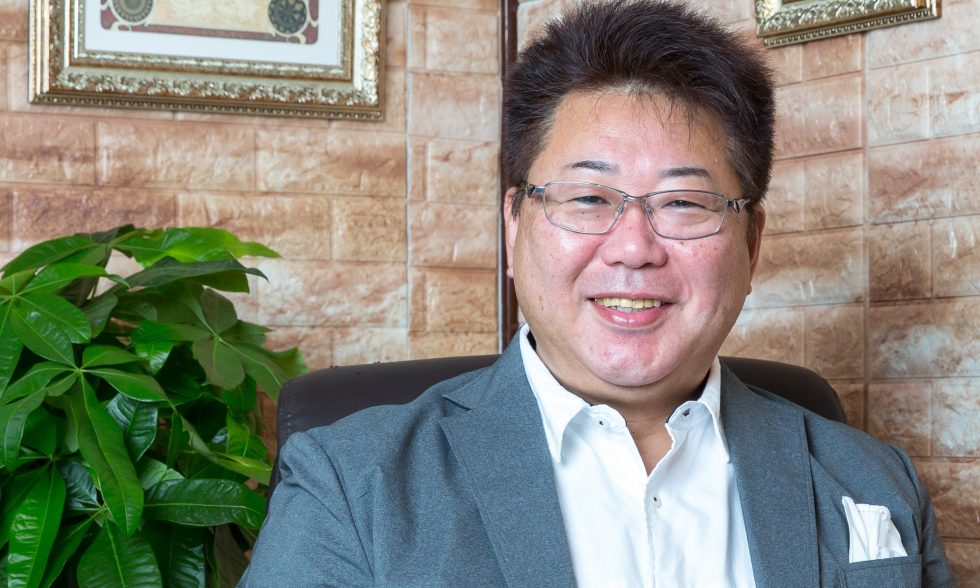
ディーズビジネスコンサルティング 佐藤
お問い合わせは、下記ホームページのお問い合わせをクリック。
※モバイルの場合は、ブログの✉相談してみるを、クリックしてもOK。
必要事項を、ご記入ください。
内容を確認させて頂き、返信させて頂きます。
お問合せを頂いたとしても、こちらから、一方的な営業メール、電話、訪問は致しません。
お気軽に、お問合せを。