作業を時間で捉える…改善ポイントの可視化
改善
2022.12.02
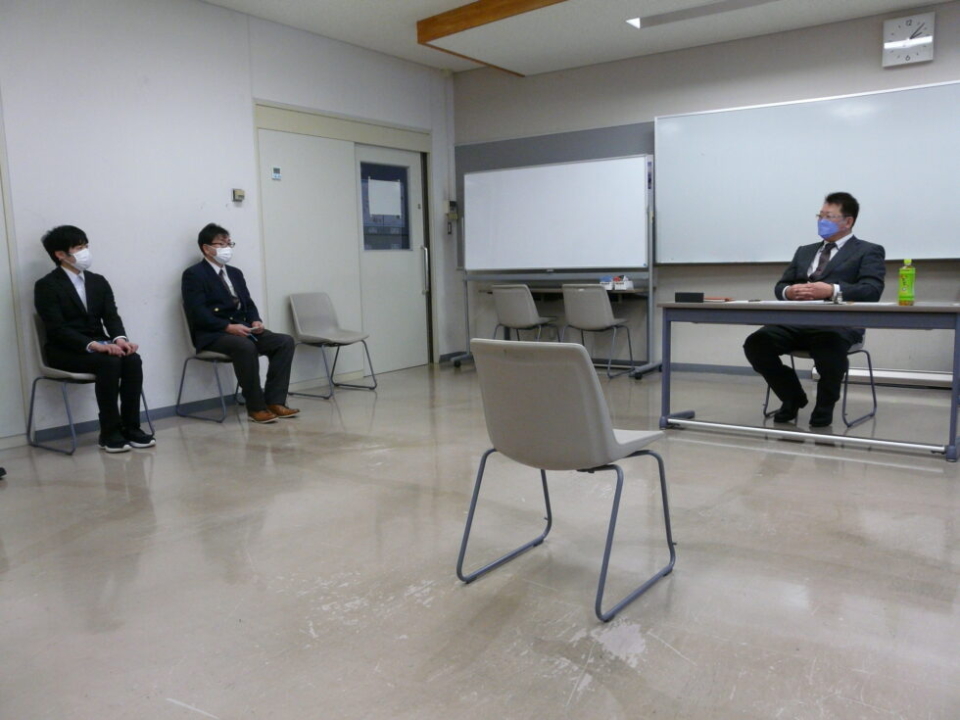
地域活性化の為に魅力ある地方企業づくりのお手伝いをさせて頂く、
ディーズビジネスコンサルティングの佐藤です。(‘◇’)ゞ
「改善して生産性上げるぞ!」
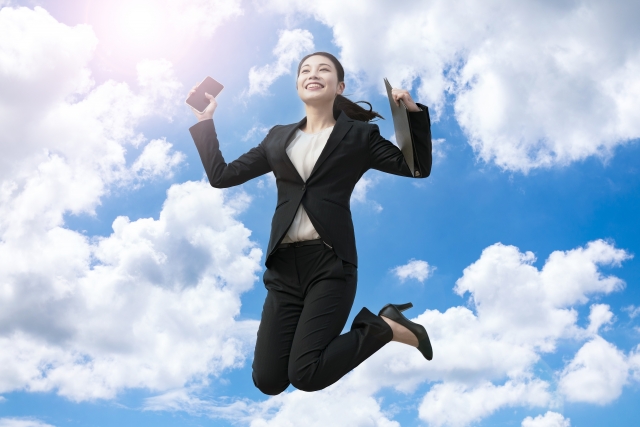
現状より、生産性を上げていく活動が改善。
改善が進まないと、利益は減る方向にシフトします。
原価が上がり、売価が下がるのが基本的な傾向ですから。
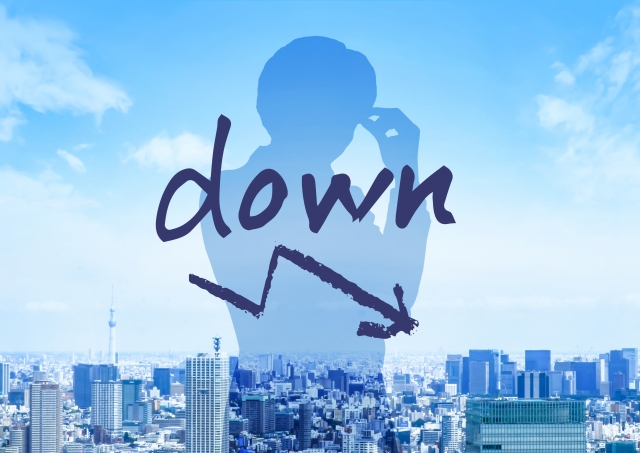
原価が上がったから、売価上げる…中々認められないですよね。
だから、原価を下げる活動である改善活動は、利益確保の為に取り組むべき行動なのです。
生き残りの為の法則と言えます。
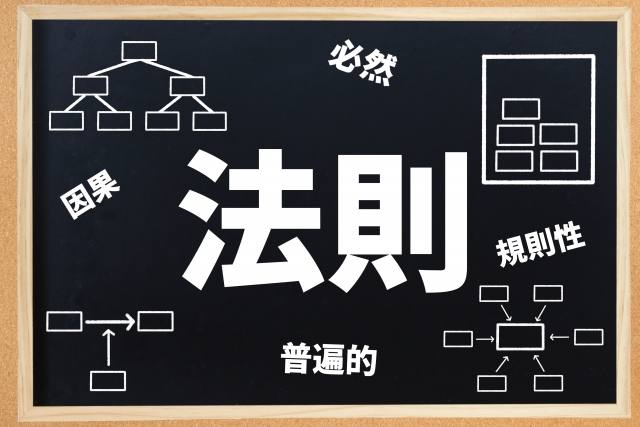
生産性の改善について、考えていきましょう。
ポイントとなるのは、どこを改善すれば良いのかを可視化すること。
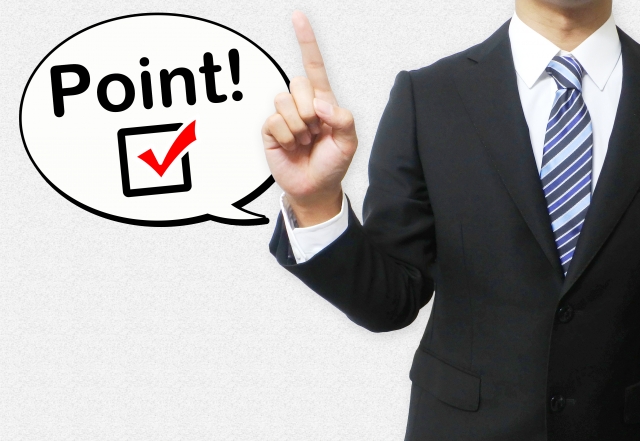
例えば…
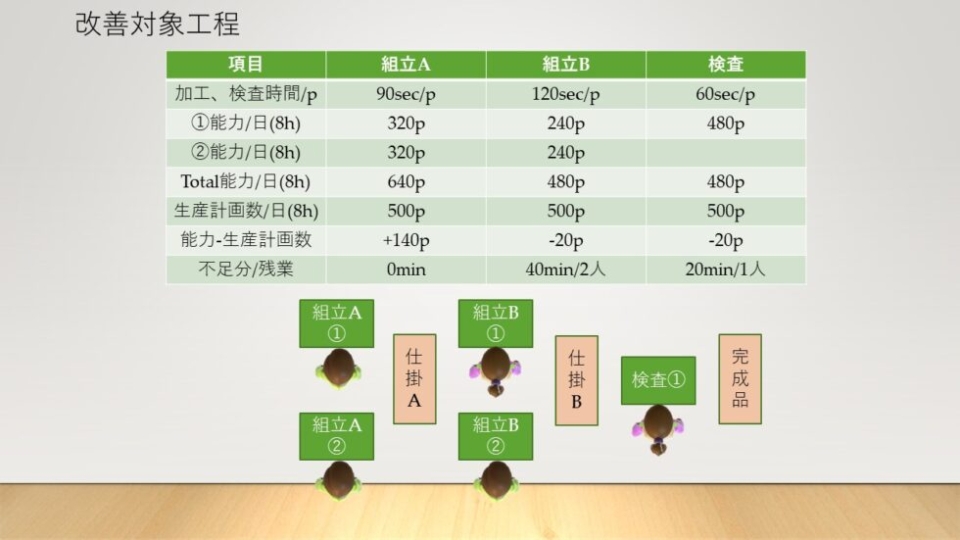
現状把握として、項目を選定して、数字で表してみましょう。
どこに、課題があるのかを可視化する。
上記の場合、組立B、検査の能力不足が課題。
なぜそうなるのかが、一個当たりの加工、検査時間が長いになります。
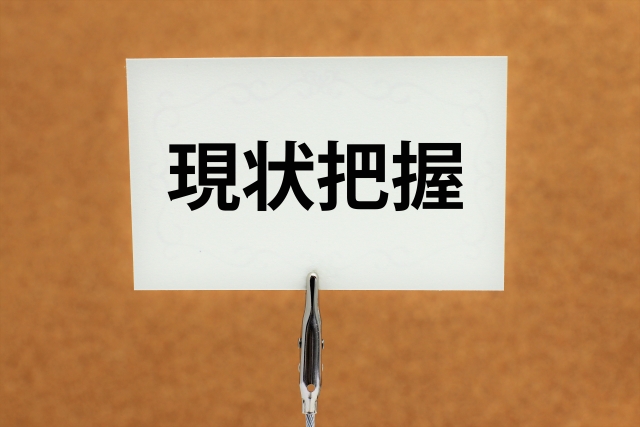
どうやって改善を進めるか?
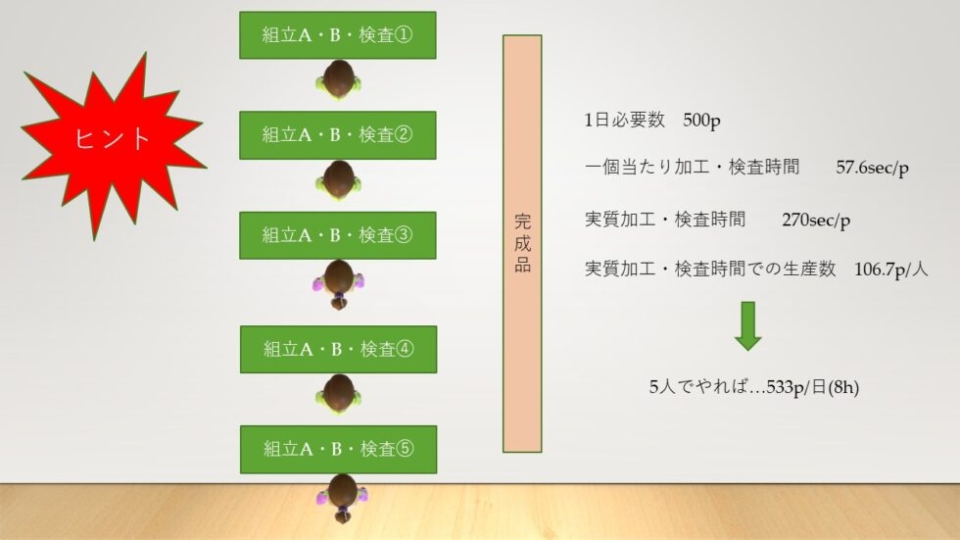
一日の必要数が500p。
それを8時間(480分、28,800秒)で、投下人員5人でできれば、現状の不足分対応で実施している残業が無くなる。
サイクルタイム(投下工数÷必要数)を求めれば、28,800秒÷500p=57.6秒/pとなります。
組立A・B・検査のトータル工数は、90秒/p+120秒/p+60秒/p=270秒です。
投下工数÷トータル工数を求めれば、28,800秒÷270秒/個=106.7p/日となります。
工程毎に分割していた人員配置を、一人完結にしたら?
106.7p/日×5人で、533p/日ができる計算です。
組立Aの能力過多を、利用した改善です。
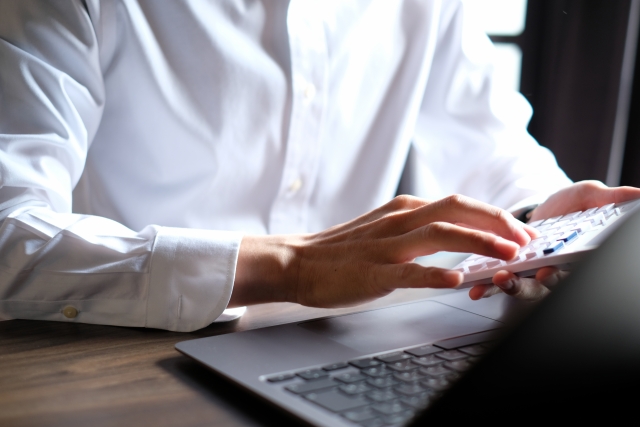
改善を進めるには、課題に気付く必要があり、その為の可視化は「改善の基礎」です。
今の工程を、棚卸しして、実際に表記してみる。
課題を明確にする。
基礎が解かれば、アレンジも可能ですよね。
5人ではなく、4人でやる為には?
どこの数字を、どれだけ変えればできますか?
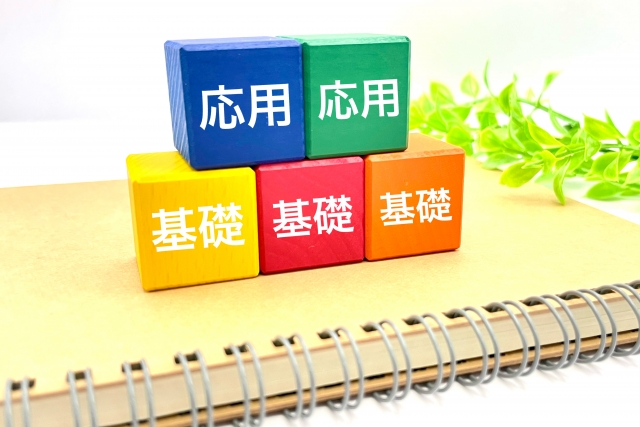
こんな課題を解決したい…、ぜひ、ご相談下さい。
儲かる仕組みづくりの、お手伝いをさせて頂きます。
See you tomorrow ♬
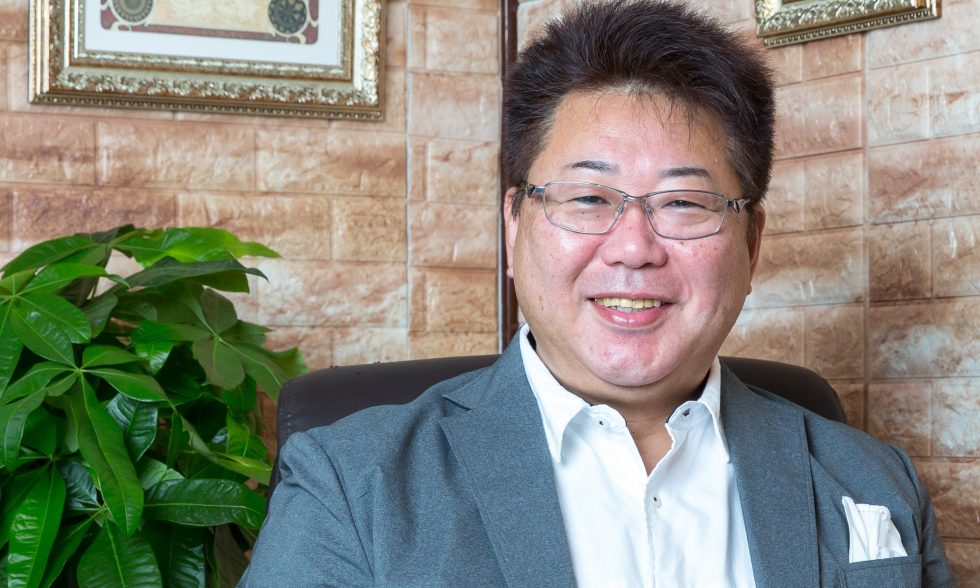
ディーズビジネスコンサルティング 佐藤
お問い合わせは、下記ホームページのお問い合わせをクリック。
※モバイルの場合は、ブログの✉相談してみるを、クリックしてもOK。
必要事項を、ご記入ください。
内容を確認させて頂き、返信させて頂きます。
お問合せを頂いたとしても、こちらから、一方的な営業メール、電話、訪問は致しません。
お気軽に、お問合せを。