いつもと変わらないのに…解決できない品質問題
品質
2023.06.15
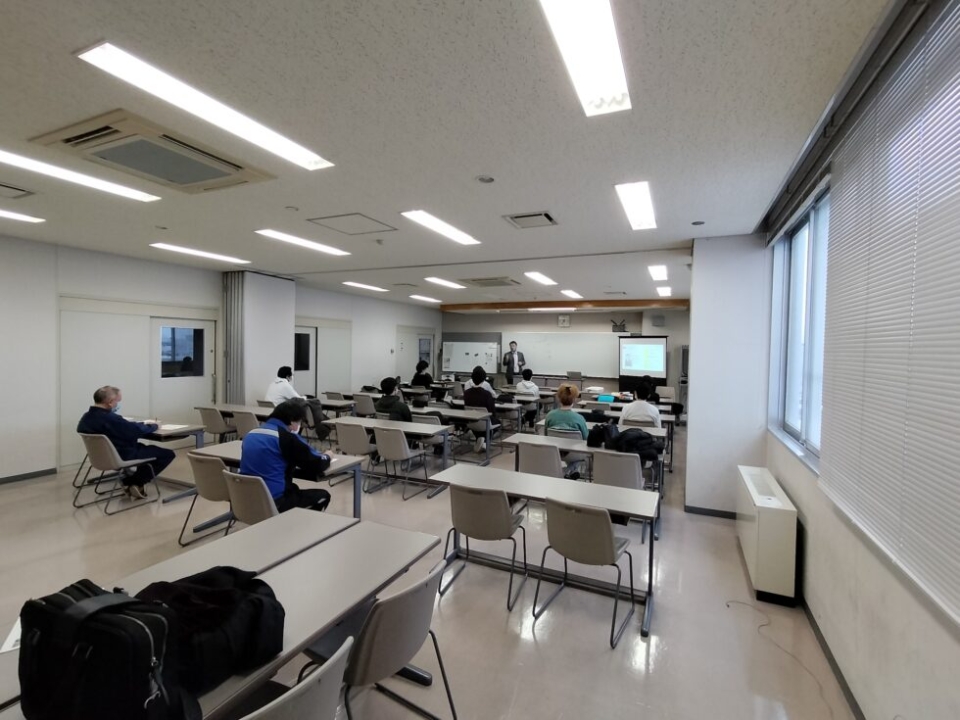
地域活性化の為に魅力ある地方企業づくりのお手伝いをさせて頂く、
ディーズビジネスコンサルティングの佐藤です。(‘◇’)ゞ
「いつもと変わらないのに、なんで不良が増えたんだ?」
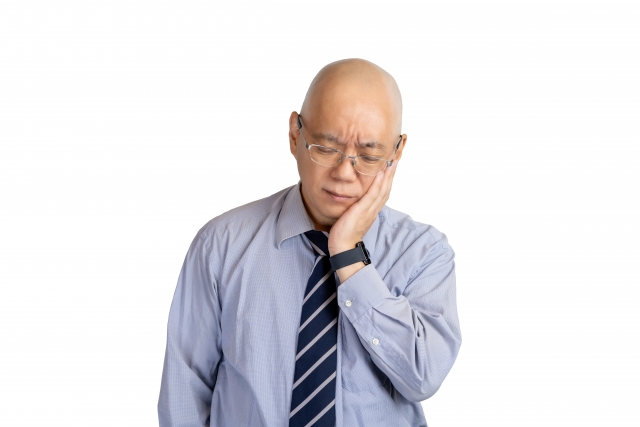
突発不良ですか?
何も変わっていない?
それは管理すべきポイントに、気が付いていないのでは?
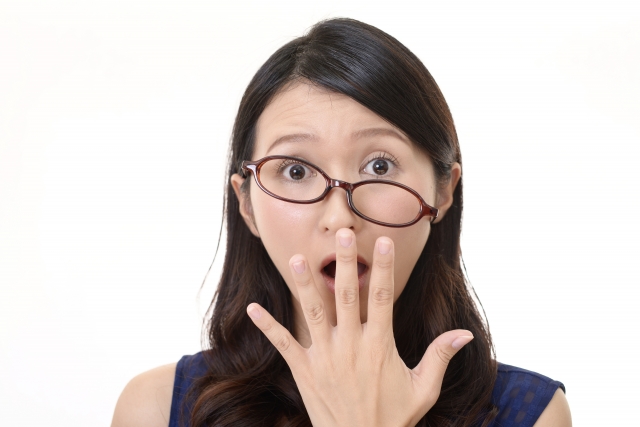
不良ができるには、必ず原因があります。
それは物理的な変化が起きている…その物理的な変化が、本来管理すべきポイントです。
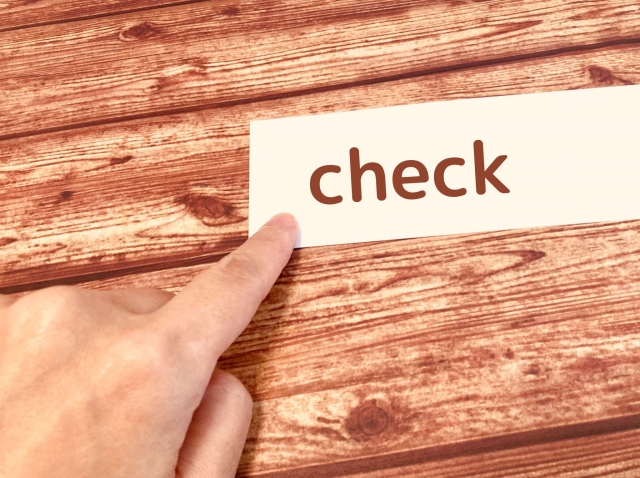
例えば…
ネジの締め付けがバラついてしまう不具合が発生したとしましょう。
正しい作業手順に沿って仕事をしている。
現状の管理ポイントは、電動ドライバーで、既定のトルクまでネジを締め付ける。
「あぁ、疲れたな…今日はしんどい」
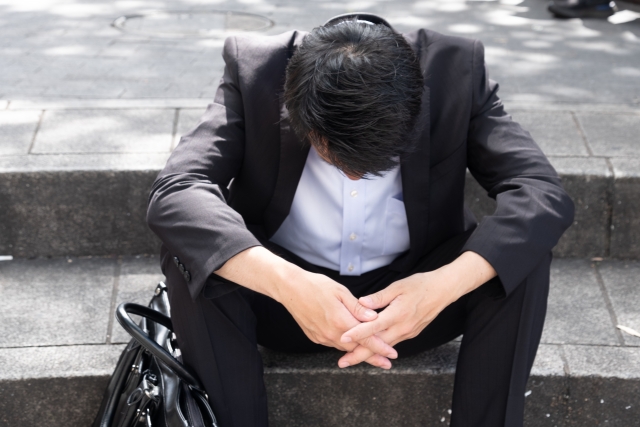
例え、そう思っていても、ルール通り電動ドライバーを使って既定のトルクまでネジを締めていれば、不良にはなりません。
「電動ドライバーの調子悪いな…まぁ、大丈夫だろ…報告するの面倒だし」
これは物理的な変化が現れています。
電動ドライバーの調子が悪いというツールの変化。
このまま使い続ければ、「ネジの締め付けがバラつき、不良になる」可能性が高い。
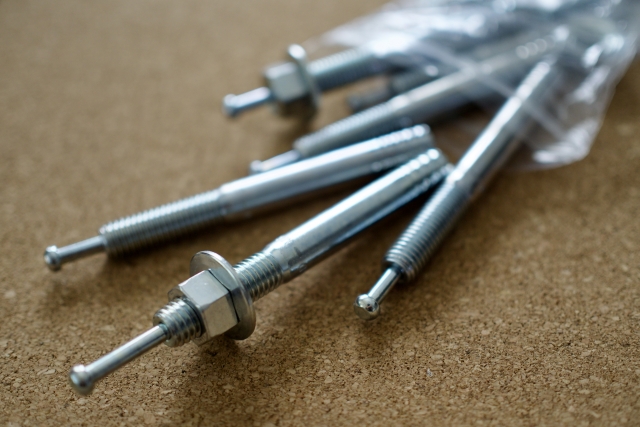
この問題に気付く為には?
・始業時、休憩明け、終業時点検で、電動ドライバーの状態を確認する→定期トルクチェック(数値化)
ツールの状態が正しいことを担保する為の管理が必要。
これを実施しないと作業できないルールとする。
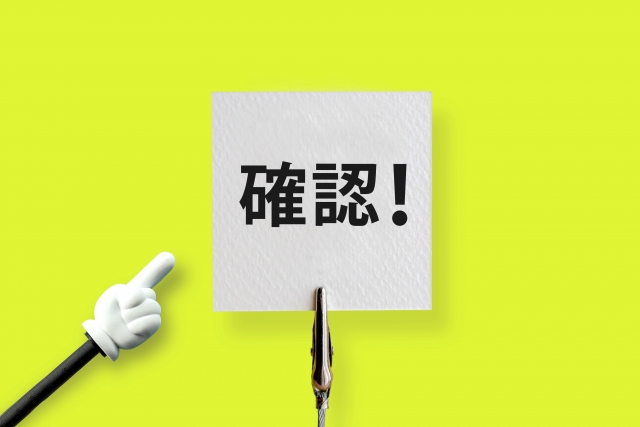
不良に対して原因を追究する為に有効なツール。
「特性要因図」を活用しましょう。
4M(人・材料・方法・設備)に大項目を分類し、それぞれに考えられる原因を書き込む。
必ず、物理的な原因に着地することが基本。
例えば先ほどのケースで言えば…
○→方法→電動ドライバーの状態確認のルールが不適切
✕→人→電動ドライバーの調子が悪いのに、打ち上げなかった
✕の人の責任は物理的な原因とは言えません。
これを原因にして報告書を作れば、「人への注意指導」が対策となり、結果再発するでしょう。
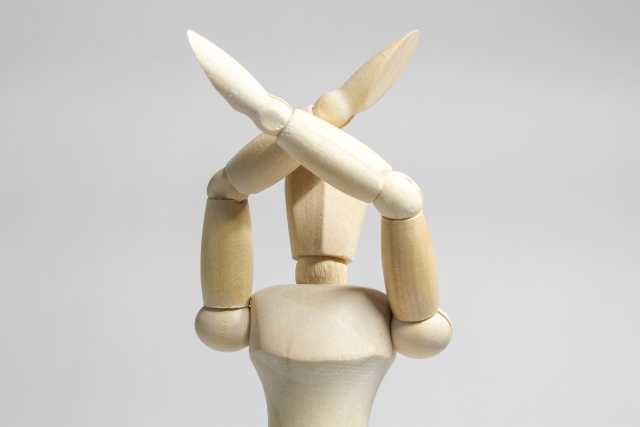
いつもと同じ、何も変わっていない…何か物理的変化が起きなければ不良にも変化は現れない。
度々、突破不良が出るなら、物理的変化に気付かず工程設計をしていると考えましょう。
人・材料・方法・設備のいずれかに起きている物理的変化。
場合によっては、単体ではなく、複合しているケースもあります。
品質問題解決において、「いつもと同じ、何も変わっていないのに出た」は、あり得ないと考えて行動しましょう。
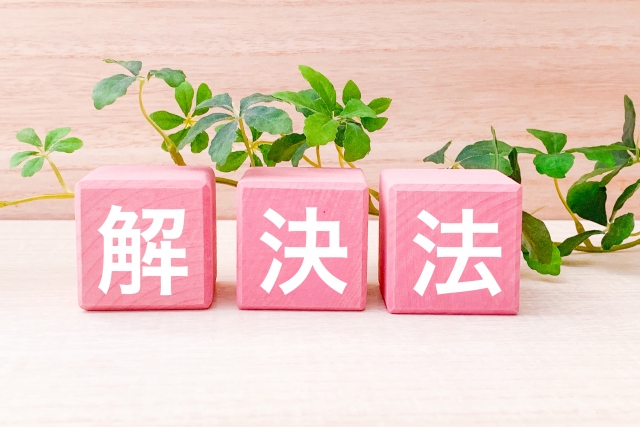
こんな課題を解決したい…、ぜひ、ご相談下さい。
儲かる仕組みづくりの、お手伝いをさせて頂きます。
See you tomorrow ♬
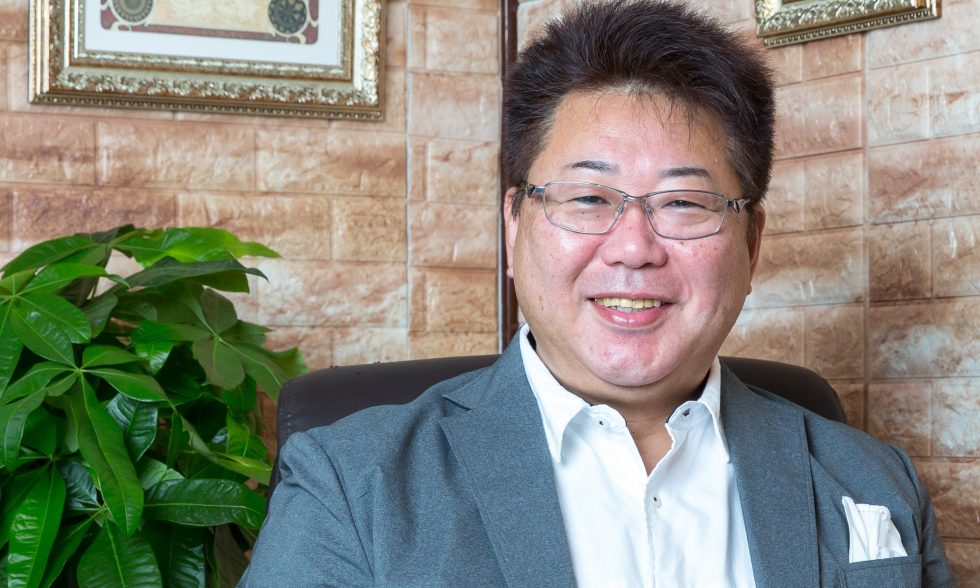
ディーズビジネスコンサルティング 佐藤
お問い合わせは、下記ホームページのお問い合わせをクリック。
※モバイルの場合は、ブログの✉相談してみるを、クリックしてもOK。
必要事項を、ご記入ください。
内容を確認させて頂き、返信させて頂きます。
お問合せを頂いたとしても、こちらから、一方的な営業メール、電話、訪問は致しません。
お気軽に、お問合せを。