作業改善…正解は1つではない、工程毎にあったやり方を考えることが、真の改善に
改善
2022.01.05
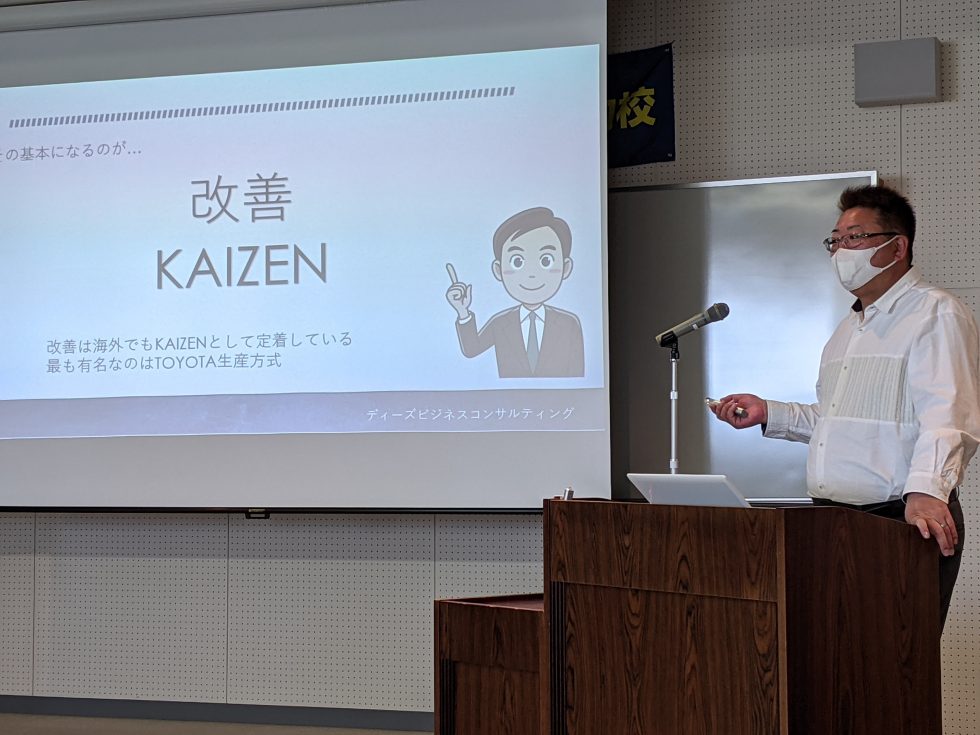
地域活性化の為に魅力ある地方企業づくりのお手伝いをさせて頂く、
ディーズビジネスコンサルティングの佐藤です。(‘◇’)ゞ
社内の改善活動、順調ですか?
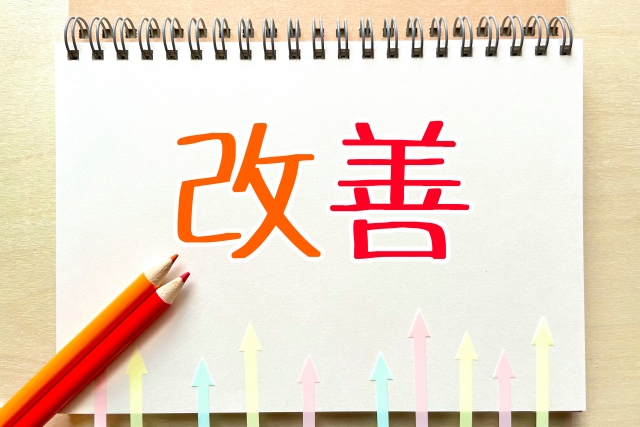
売り上げの変動、原価の変動は必ずあるもの。
売り上げ確保の為にコストダウンする。
人件費も年率で上がる。
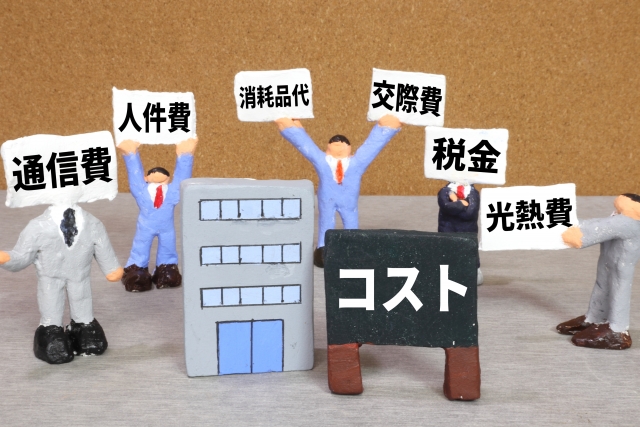
去年と同じ体制では、実質後退していることになります。
従って、利益確保の為には、原価改善が必要。
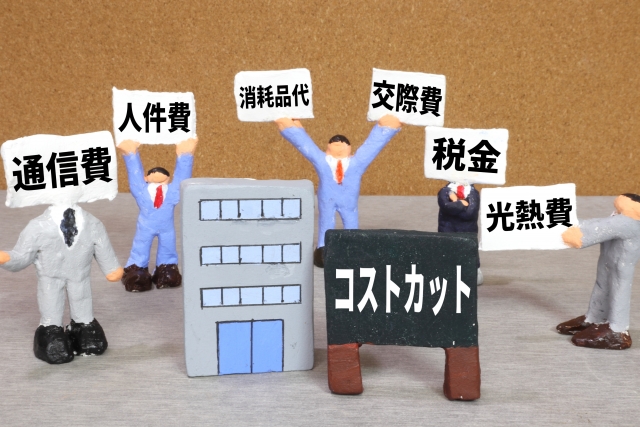
改善は、事業継続の上で、必要な行為です。
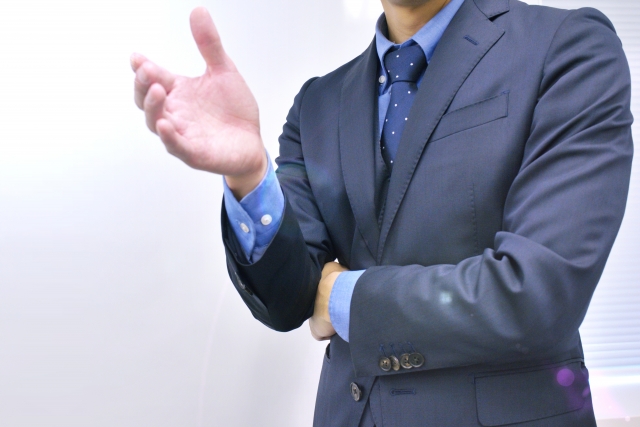
一口に改善と言っても、決まりごとはあるの?
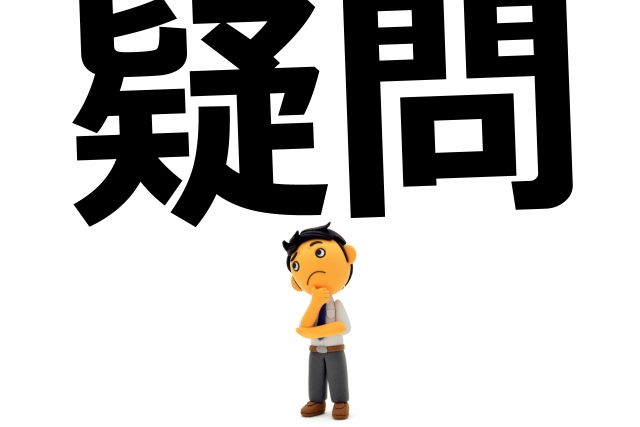
決まりごと…考え方という点ではあると言えます。
無駄の見方とか、見える化とか、人の動作とか…etc。
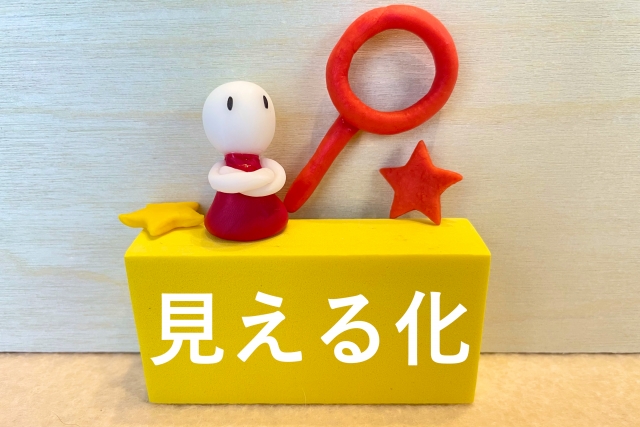
でも、この場合はこのように改善する…という答えがあるものではありません。
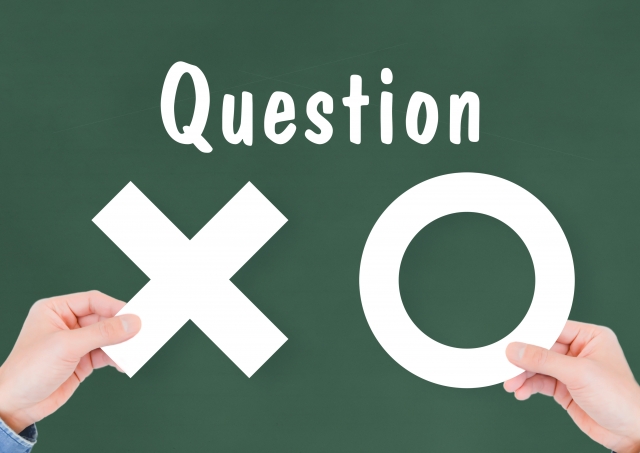
環境、条件等の事情により、正解は変化するもの。
同じ職場であっても、時間経過で正解が変わることもあります。
環境、条件が変わることによって。
だから、一度改善したから恒久的に効果が出る…とは、限らない。
常に、今、最も良いやり方は?を、考え続けなければなりません。
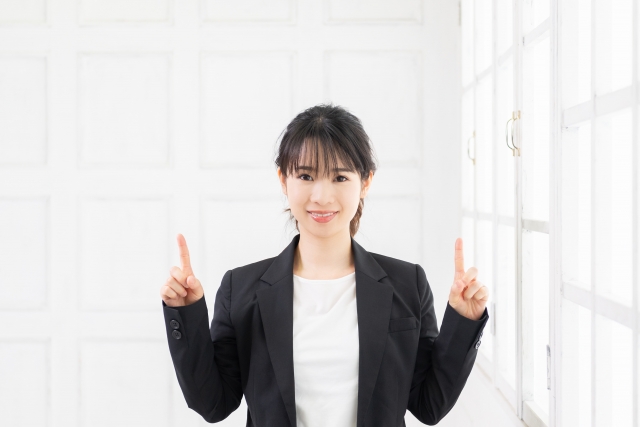
例えば、このようなケース。
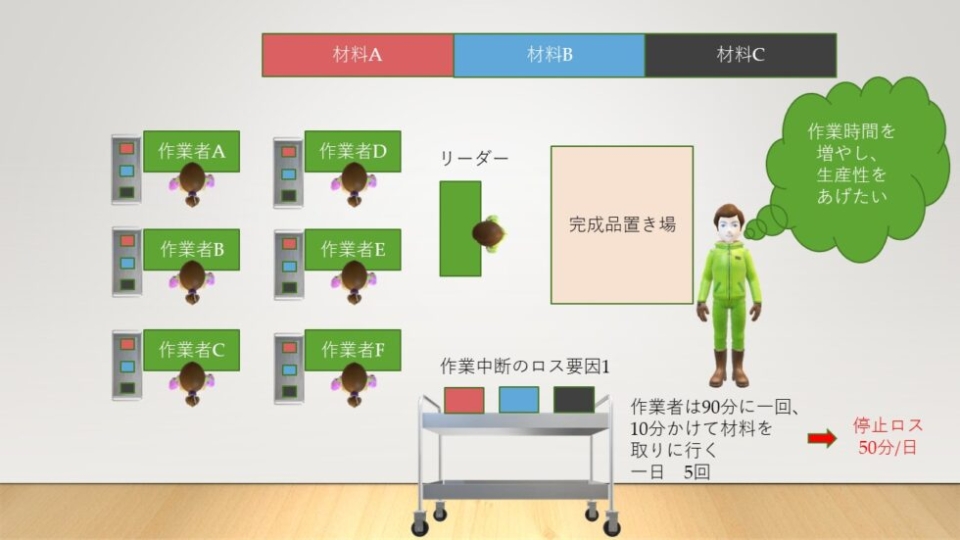
この現場のリーダーは、生産性を向上させたいと考えている。
その為に、作業者の作業時間を増やしたい。
着目したのは、材料の入手時に、50分/日のロスがあること。

材料を取りに行く回数を減らす…という切り口の場合。
台車のサイズアップで、一回での積載量を変えれば…これも一つの改善。
改善効果は、減らした回数×6人分。
間違いではありません。
ただし、環境、条件に適しているか?
どのサイズにするか?
投資vs効果は?
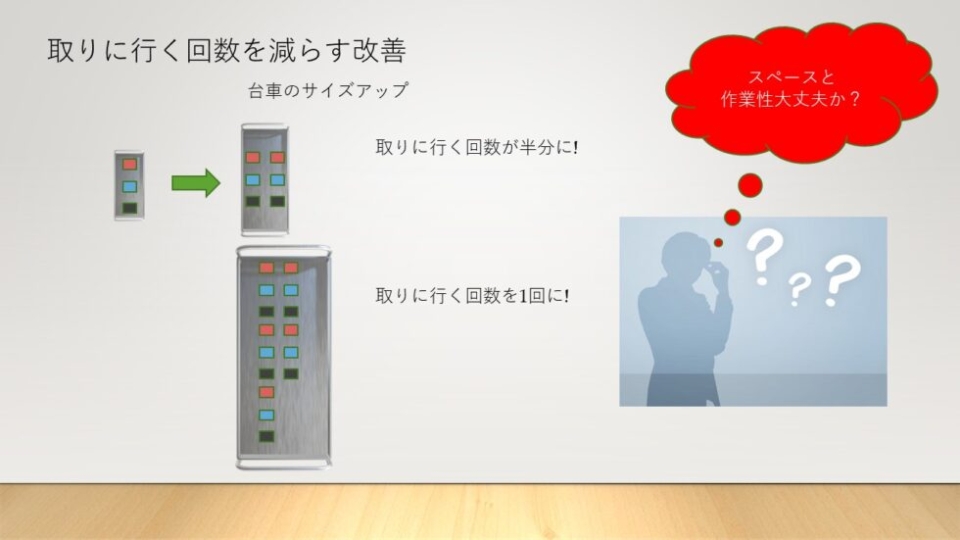
作業者が取りに行かなくて良い改善。
作業者の仕事から、他者への仕事へ振り分ける。
例えば、リーダーが全ての配膳作業を対応。
これによる改善効果は、作業者6人×50分で、300分/日
間違いではありません。
ただし、リーダーの仕事量は増えるので、先にリーダーの時間を作る必要があります。
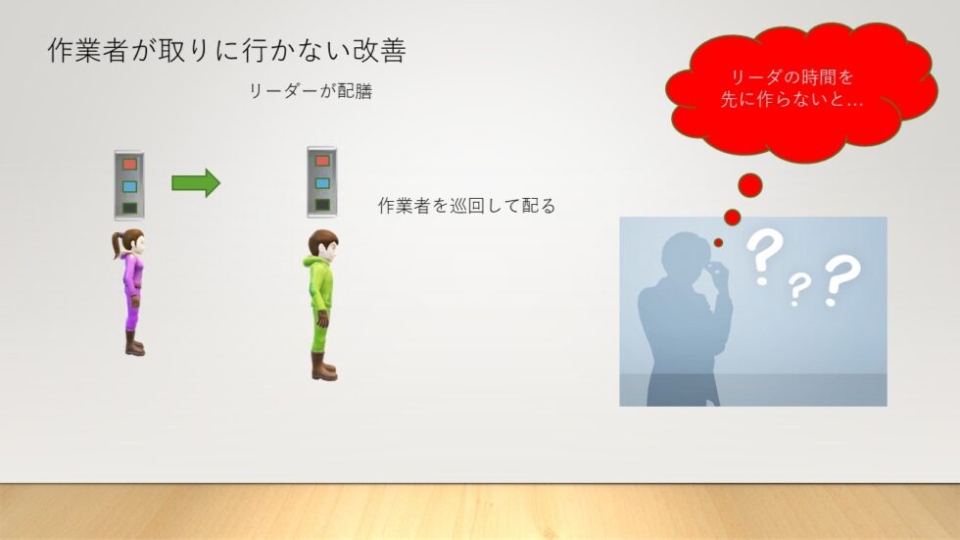
他にも、色々な改善ができるケース。
最も改善効果の大きいものを選ぶ。
A社では台車サイズアップだが、B社ではリーダー配膳かもしれません。
二つの改善を、合算する手もあります。
それぞれの環境、条件によって、正解は変わる。
他にも、色々と考えられます。
ちょっと考えてみませんか?
自社なら、どういうパターンがあっているか?
または、自社はどうやって材料を取り扱っているか?
同じように、改善したい…という工程を、イメージしてみましょう。
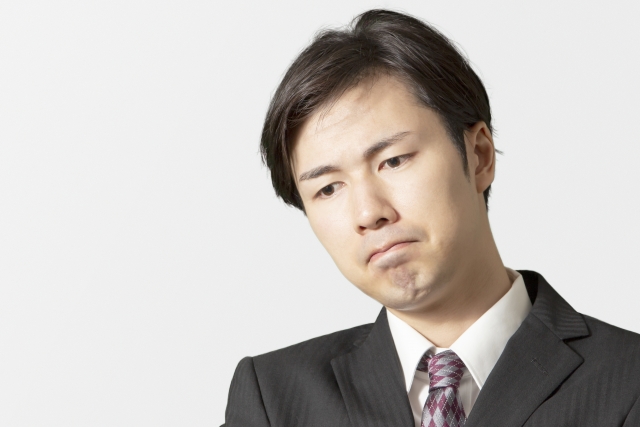
今のやり方が一番いい。
そう考えたら、改善の発想は生まれません。
現状を否定することが、改善の第一歩。
変えない、変わらない…それもリスクだと思いませんか?
リターンの幅が目減りしていく訳ですから…。
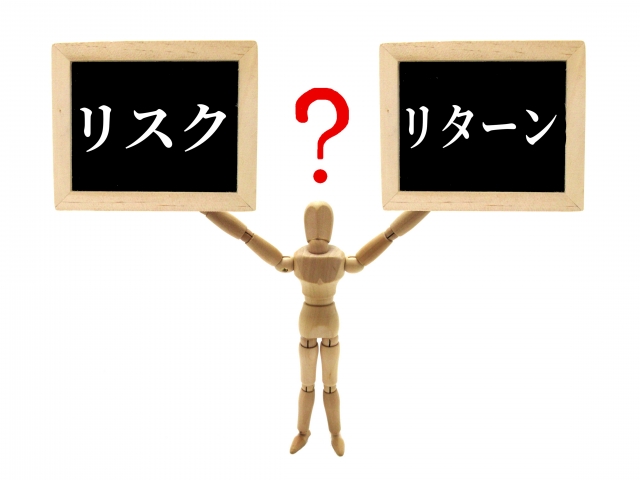
こんな課題を解決したい…、ぜひ、ご相談下さい。
儲かる仕組みづくりの、お手伝いをさせて頂きます。
See you tomorrow ♬
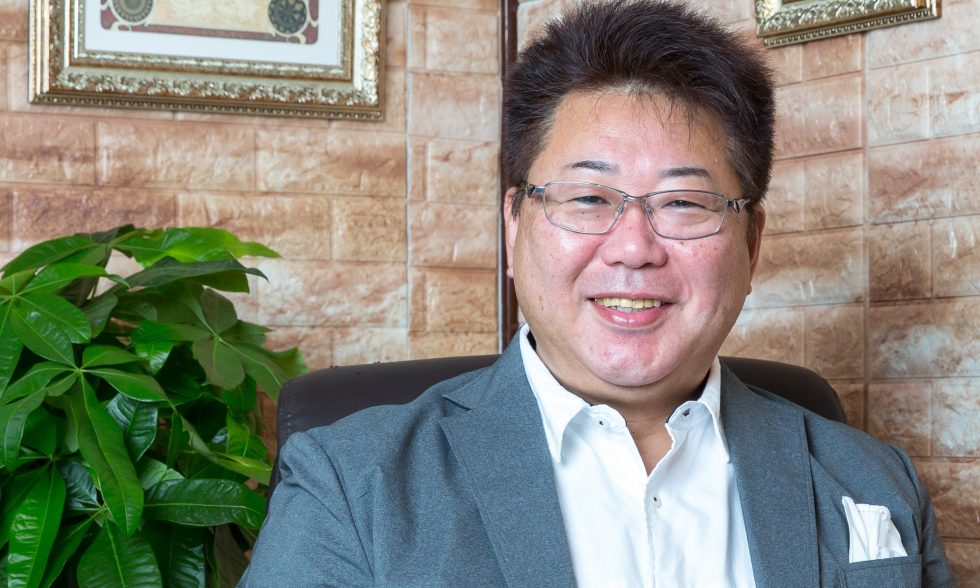
ディーズビジネスコンサルティング 佐藤
お問い合わせは、下記ホームページのお問い合わせをクリック。
※モバイルの場合は、ブログの✉相談してみるを、クリックしてもOK。
必要事項を、ご記入ください。
内容を確認させて頂き、返信させて頂きます。
お問合せを頂いたとしても、こちらから、一方的な営業メール、電話、訪問は致しません。
お気軽に、お問合せを。