原因は作業ミス…注意、指導しますの報告書って?
品質
2022.12.09
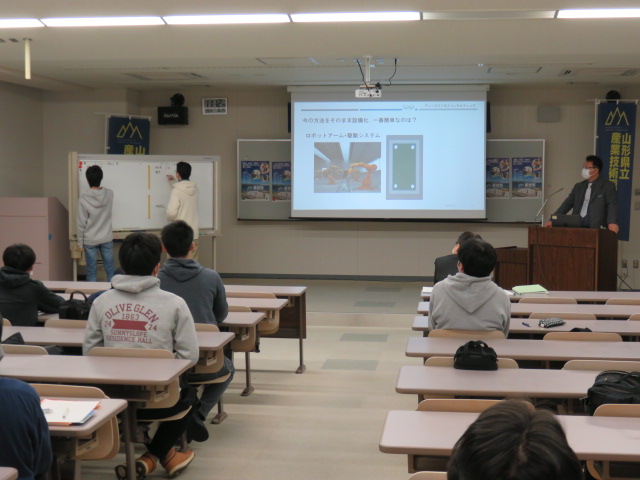
地域活性化の為に魅力ある地方企業づくりのお手伝いをさせて頂く、
ディーズビジネスコンサルティングの佐藤です。(‘◇’)ゞ
「この問題の原因は、作業者のミス…注意指導します」
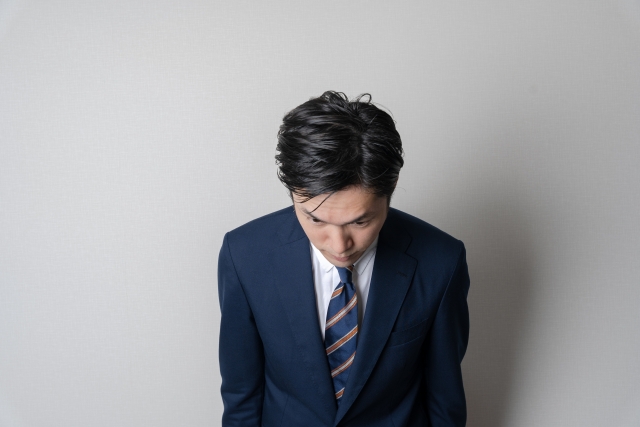
クレーム報告書や工程内異常の報告書に、良くあるパターン。
更には社内で起きた納期トラブルや発注ミスで、上司に報告する時も良く聞きますよね。
でも、そもそも作業ミスって本当の原因でしょうか?
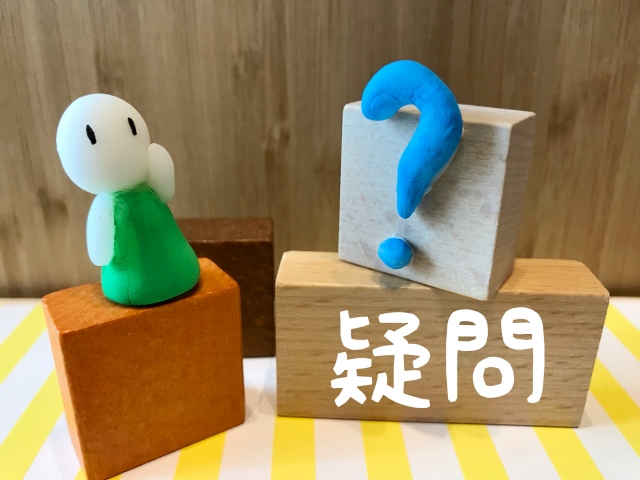
原因を人のミスで決めつけて、注意、指導を対策にすることに慣れると、再発リスクは高くなります。
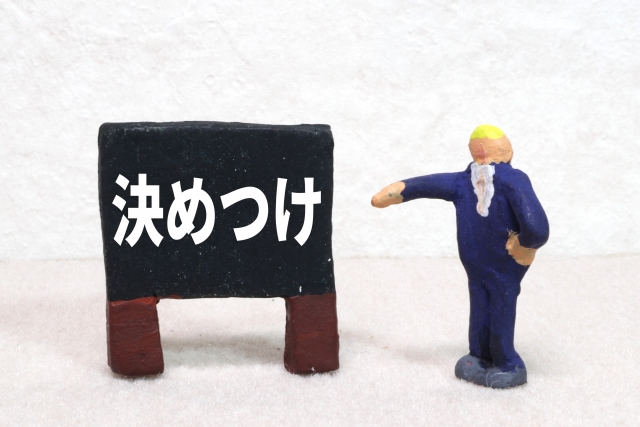
例えば…
・検査での見逃しで、不良品が流出した
検査基準にあるものを見逃したから、検査員=人の問題
☆検査時間は、いつもと一緒だったのか?
☆検査環境は、当該不良を見つけやすいか?
☆検査方法は、当該不良の検出に適しているか?
☆…etc
・適切な清掃をしていなかったため、発生した
清掃方法は決まっていたから、作業者=人の問題
☆清掃時間は、いつもと一緒だったのか?
☆清掃方法通りにやれば、綺麗になるのか?
☆清掃方法のツールは、時間は…それで本当に綺麗にできるのか?
☆…etc
こんな風に考えたら、どうなりますか?
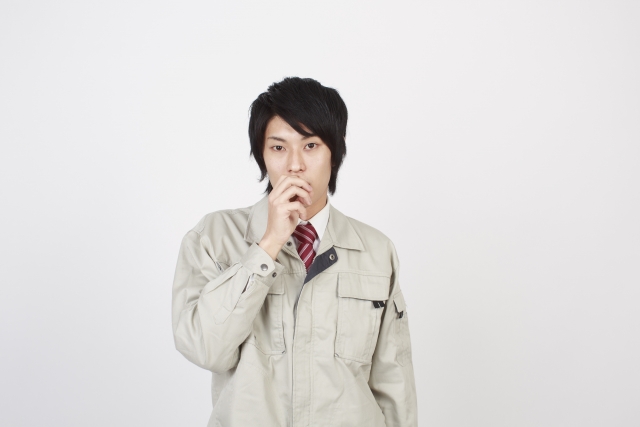
人がミスした…これで、終わると、ミスが起きた背景や現状の方法に対する課題へ辿り着けない。
これでは、再発もします。
また、類似した工程でも同じようなことが、繰り返し発生し、その都度、対処することになります。
水平展開ができないからです。

それでは、良くなると思えませんよね。
こういう時に使う品質改善ツールが、なぜなぜ分析や特性要因図です。
第一ステップに「作業ミス」を記載し、そこから深堀していく。
作業ミスが生まれる真因を追求する。
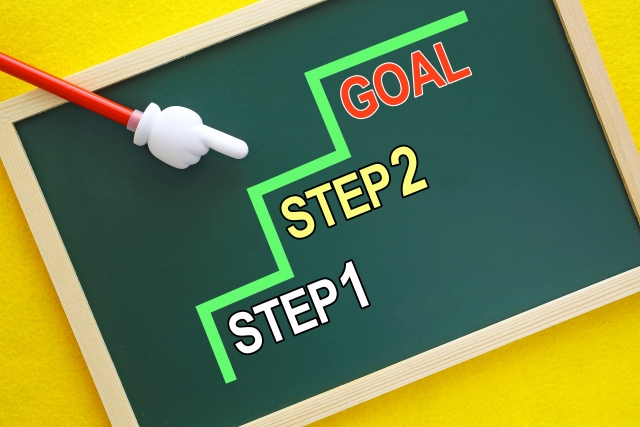
方法や条件での課題を整理せずに、人要因で片付ける発想をアップデートしましょう。
注意、指導が対策なら、真因に辿り着いていないと考えましょう。
本当にやるべきことが、先にある。
クレーム、工程内不良や、社内で起きる様々なトラブル…全て同じです。
過去に作成されたクレーム報告書、工程内異常報告書の対策を見直してみませんか?
対策「作業者、検査員への注意、指導」となっているもの、どれだけあるでしょう?
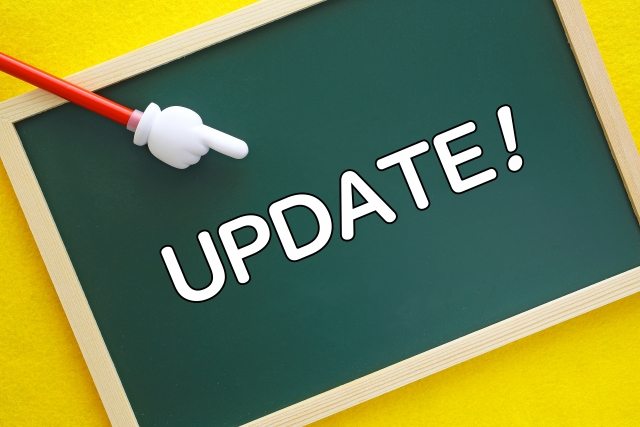
こんな課題を解決したい…、ぜひ、ご相談下さい。
儲かる仕組みづくりの、お手伝いをさせて頂きます。
See you tomorrow ♬
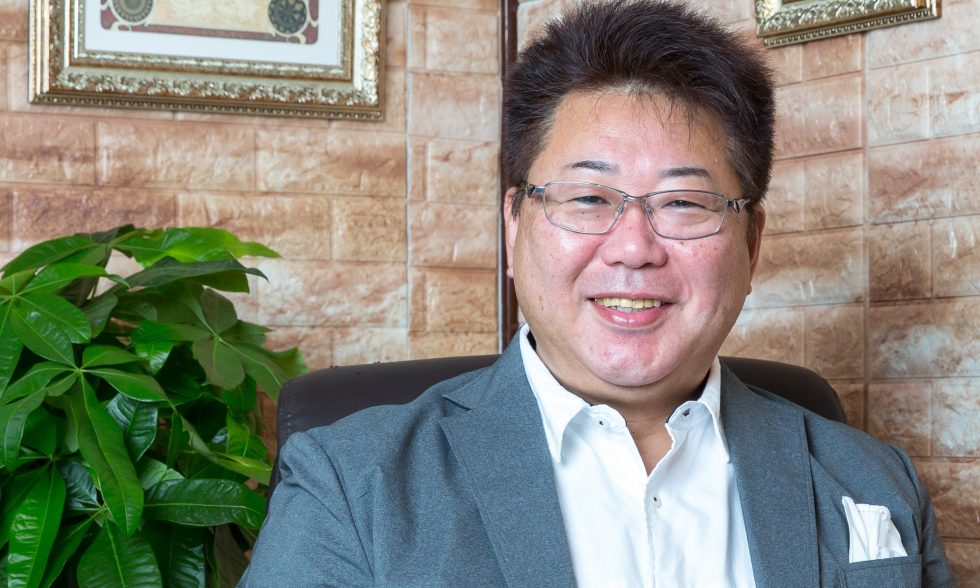
ディーズビジネスコンサルティング 佐藤
お問い合わせは、下記ホームページのお問い合わせをクリック。
※モバイルの場合は、ブログの✉相談してみるを、クリックしてもOK。
必要事項を、ご記入ください。
内容を確認させて頂き、返信させて頂きます。
お問合せを頂いたとしても、こちらから、一方的な営業メール、電話、訪問は致しません。
お気軽に、お問合せを。